- Related articles
- All Cisco CWDM-SFP10G-1610's information (List price, Specs, Datasheet PDF, Compatibility
- Applicable to 100BASE-F Standard Optical Transceiver Models
- Optical Transceivers for Cisco SG550XG-24F-K9-UK Switch
- Optical Transceivers for Cisco N9K-C9396TX= Switch
- All Cisco WS-G5487’s Information (Overview, Features, Data Sheet PDF, Price, Specification
- Optical Transceivers for Cisco WS-C2960XR-24TD-I Switch
- Optical Transceivers for Cisco WS-C3560E-24TD-SD Switch
- All Cisco DWDM-XENPAK-31.90's information (List price, Specs, Datasheet PDF, Compatibility
- Optical Transceivers for Cisco WS-C2960S-48LPD-L Switch
- The Things You Need to Know about 100BASE-X Ethernet Standards

We all know that fiber jumpers at both ends of the cable are fitted with connector plugs. When selecting the fiber jumper, in addition to considering the connector, identifying the merits of the cable is also extremely important.
Fiber optical cable is a protective sleeve of the bare fiber, which is made up of four parts of the fiber, tight layer, aramid yarn and outer sheath from the inside to outside. The optical fiber is made up of three parts of the core, cladding, and coating from the inside to the outside of three parts, so how to identify the merits of cable?
1. Looking at outer jacket material
1). Indoor fiber optical cable is generally made of polyvinyl chloride (PVC) or flame-retardant polyethylene or polyurethane (LSZH) and other materials with smooth, soft and flexible appearance, easy to peel; poor-quality optical fiber tegmen is very poor in fineness and is very easy to have adhesions with the outer sheath, aramid yarn.
2). Outdoor cable’s outer jacket uses high-quality black polyethylene (HDPE, MDPE), and has the smooth and bright skin, uniform thickness with no bubbles after it’s cabling; low-quality fiber optical cable skin is generally made of recycled materials with rough skin. Raw materials have many impurities. A closer look can find a lot of very small pits in the cable sheath. The cable jacket will be white back and forth for several times and will be cracking with water seepage if lying for some time.
2. Looking at fiber quality
Regular fiber optical cable manufacturers generally use A-class core; low-cost low-grade cable often uses C-class, D-class fiber or unknown smuggled fiber. Because of the complex sources, these fibers often get damp and discolor, and multimode fibers are also often mixed with single-mode fibers.
And due to the lack of necessary testing equipment, the general small factory cannot make judgments on the quality of fiber. Because the eye cannot identify such a fiber, people often encounter too narrow bandwidth, short transmission distance, uneven thickness, and no connection with pigtail, lack of flexibility for fiber, breakage with a little bend and other problems.
3. Looking at the wire color
Outdoor fiber optical cable steel wire of formal manufacturers is treated by phosphorization with the gray surface, which will not increase the hydrogen loss with no rust but high strength if into the cable; low-quality fiber optical cable is generally replaced by thin wire or aluminum wire with white surface, can be bent in the hand at will. With this steel wire, the production of fiber optic cable in the future will produce additional hydrogen loss, and for a long time, will lead to two ends of the fiber box in rust and breakage.
4. Looking at the fiber tube material
The loose tube where fiber optical cable is should use PBT material. Such a tube has high strength, not easy to deformation, and is anti-aging; poor-quality cable usually uses PVC material production tube, which is very thin and soft so as to be flat if pinching. Like the beverage pipette, it cannot keep a good protection of optical fiber.
5. Looking at the quality of fiber unto
Outdoor fiber unto within the fiber can effectively prevent the fiber the crazing, hydrogen loss and fracture generated by water vapor. Poor fiber uses the fiber unto rarely which can be observed by the naked eye with a little bubble. If the using poor quality fiber unto, it will seriously reduce the fiber optical cable life.
6. Looking at the thickness of aramid
Aramid, is a high-strength chemical fiber. Indoor cable and all dielectric self-supporting optical fiber cable (ADSS) uses aramid yarn as a reinforcement. Due to the higher cost of aramid, low-grade indoor cable generally makes the thin outer diameter, so that costs can be saved by reducing the number of aramids. But such a fiber cable in the pipe is easy to be pulled off.
7. Looking at the quality of cable unto
Usually, high-quality cable unto mixed evenly will not appear separation phenomenon after long-term use. The poor-quality cable unto is easy to volatilize and not filled with, affecting the moisture resistance of fiber optical cable.
In summary, for the cable part in the fiber jumper, the real differences in merits are derived from its structural design, timber materials, and production processes. For the cable itself, its value is not large, but the cost during the laying process (buried, overhead, piped, etc.) is very alarming and time-consuming and effort-consuming. In addition, the entire communication link is the basic medium, so once there is a problem, no matter how expensive the hardware at both ends are, the whole system will be completely paralyzed, and the repair cycle will be very long, resulting in huge losses.
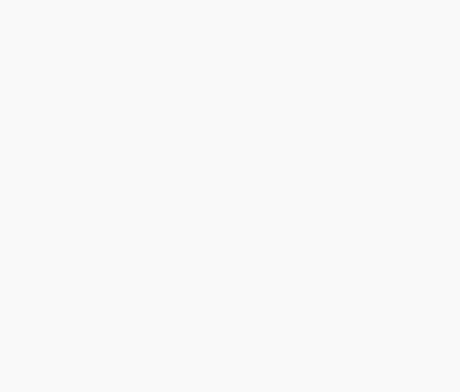