- Related articles
- Optical Transceivers for Cisco WS-C2960C-8PC-L Switch
- Optical Transceivers for Cisco SG200-26FP-UK Switch
- Optical Transceivers for Cisco N9K-X9636PQ= Switch
- All Cisco GLC-BX-U's information (List price, Specs, Datasheet PDF, Compatibility matrix)
- What is Linux PAM module?
- What is 1000BASE T Transceiver?
- Optical Transceivers for Cisco SLM2024T-EU Switch
- All Cisco CWDM-SFP-1590's information (List price, Specs, Datasheet PDF, Compatibility mat
- What is PAM Authentication?
- Optical Transceivers for Cisco WS-C3750E-24TD-SD Switch

Compared with copper cable, fiber optic cable is quite fragile. Damages often happen especially during the fiber optic cable construction. This article will disclose the Seven Deadly Sins during fiber optic cable construction.
1: without cleaning the fibers before splicing
Cleaning bare fibers is a significant process before splicing fibers. The standard steps are cleaning the bare fibers at first before cutting them. Basically, nothing could be cleaner than the newly-made fiber end face, so do not clean the fibers after cutting them, otherwise, fibers would be definitely polluted or even damaged. Besides, the rapid evaporation, non-combustible precision cleaning fluid is a recommendation for cleaning the bare fibers.
2: use improper cutting tool
Smoothness of fiber end face has a vital influence on the performance of fibers welded or terminated. In the past, people used to cut fibers manually by optical fiber cleaver, which is only made by the operators who had been trained well and are skilled. Currently, with the development of technology, the modern auto-cutting tools are common in the markets; these tools can not only improve the security for operators but also provide protection for fibers. All in all, auto-cutting tools are the indispensable tool that guarantees the fiber is correctly cut with standard end face.
3: without calibration before fiber splicing
Calibrate welding machine is also quite important. Generally the intensity of electrical arc or current needs multiple calibrations to make sure the size is appropriate when welding, the mechanical strength of melting joint is strong enough and the optical performance is good enough, all of which are crucial especially when the air pressure is changing or working under high latitude. In fact, calibration is not hard to do. For most welding machines, there is auto-reminder to let you know how to do next after you place the fibers on the machine as like they are going to be welded, but it is not really needed to do welding when calibrating. After calibration finished, the welding machine would remind of finish or if you need test the whole system again.
4: slight bend happens to the fiber
Slightly bent fibers are mostly caused by the over-pressure on the fibers. Being slightly bent of fiber would result in signal quality weakening, which is hard to detect by naked eyes unless using OTDR.
5: excessive bend happens to the fiber
All the fiber optic cables have the minimum bend radius, as a result, it’s not allowed to exceed the minimum bend radius when laying fiber optic cables, otherwise fiber optic cables and fibers would be damaged.
6: repeatedly use cleaning cloth or paper
This is an easy step but also often ignored. the cleaning cloth or paper would get dirty after it is used to clean a connector, more than dirt from the connector, oil and dust from fingers would also pollute the cleaning cloth or paper. If you reuse it to clean another connector, then the pollution would pass to the connector. Therefore, repeatedly using cleaning cloth or paper is not wise to save costs, replacing with smallest cleaning cloth or paper may help to save some of cost.
7: without inspecting and cleaning connector end faces before installation
The connector end faces are also one of the places that are extremely easily polluted by dust, oil or other contaminations. Therefore, we are supposed to inspect and clean the end faces of fiber optic connectors before installing connectors. The cost of a ferrule end face tester is far less than that of twice on-site maintaining, spending a little money to do inspection and cleaning or costing more money to maintain, obviously the formerly is better.
Conclusion
All above mentioned are the persistent problems in fiber optic communication. These problems are likely to cause fiber optic network get slower and bring breakdowns, however, it’s easy to avoid them as long as fiber optic network constructors strictly follow the standard operations and pay more attention.
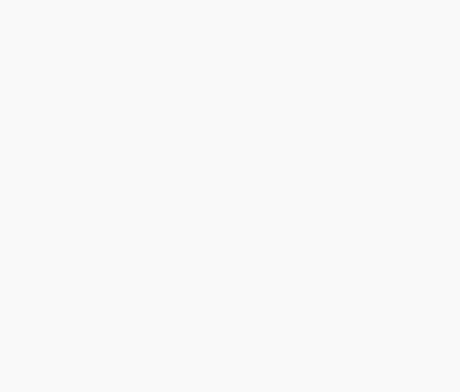